通过设计正交试验,分析了抛丸清理过程中钢丸粒度、抛丸时间等因素对铸件表面粗糙度的影响。结果表明:抛丸时间对铸件表面粗糙度的影响最大,抛丸时间越长,铸件表面粗糙度越低;其次为钢丸粒度,直径较小的钢丸有利于降低表面粗糙度;而钢丸抛射速度的影响较小。根据试验结果,对抛丸工艺进行了优化和探索。
铸件的表面质量直接影响到铸件整体的质量和性能。抛丸清理是影响铸件毛坯表面质量的最后、也是最关键的一道工序1,抛丸机利用高速旋转的叶片把钠丸高速抛掷,撞击零件表面,可以除去零件表面的粘砂、毛刺、锈蚀、氧化层;同时钢丸高速撞击会造成零件表面的晶格扭曲变形,使表面硬度增高,可以用于对零件进行表面强化3。
目前随着生产效率的提高,抛丸清理机的应用已趋于成熟,抛丸量可达20 kg/s,清理效率不断提高,铸件毛坯的表面质量也有了极大改善”。生产实践表明,弹丸粒度、抛丸时间、弹丸速度、抛射角度等因素对抛丸清理后铸件的表面粗糙度有显著影响5。筛选出对粗糙度影响较大的因素,并据此优化王艺参数,对提高铸件的质量和产能都有积极的意义。
1试验方法
本试验采用公司一直使用的铸钢丸,使用行业内常见的Q 3740E-4单吊钩抛丸机,由于抛丸器的抛射角度已经过模拟优化,本试验中角度固定。结合生产实际,本文主要研究钢丸粒度、钢丸抛射速度、抛丸时间三个因素对铸件表面粗糙度的影响。
钢丸粒度:我公司日常使用的钢丸主要有0-1.4mm和φ-1.7 mm两种规格,另有同行业的经验标明级配钢丸的清理效果优于单一粒度钢丸”,本试验将考察级配钢丸的清理效果,级配钢丸配比采用60%S200钢丸(Ф=1.7 mm) +40%S170钢丸(=1.4 mm)。
抛射速度:钢丸切向抛射速度用公式-nmD/60,求得,其中n为抛丸机转速(r/min) , D为抛丸器叶轮直径。
抛丸时间:我公司对中等箱体类铸铁件的抛丸时间一般在10min左右,试验中将以此时间长度为基准进行研究。
为优化试验过程,本文采用了正交试验,同时,设计正交表时添加了空白列以排除对粗糙度有明显干扰的因素。如上所述,该试验为4因素3水平,可采用L(3)正交表(表1)。
试验中进行抛丸的铸件选择公司产品中较为普遍的中等箱体类铸件,抛丸完成后将铸件表面与表面粗度比较样块进行对照比较,并采用粗糙度测试仪进行测量。
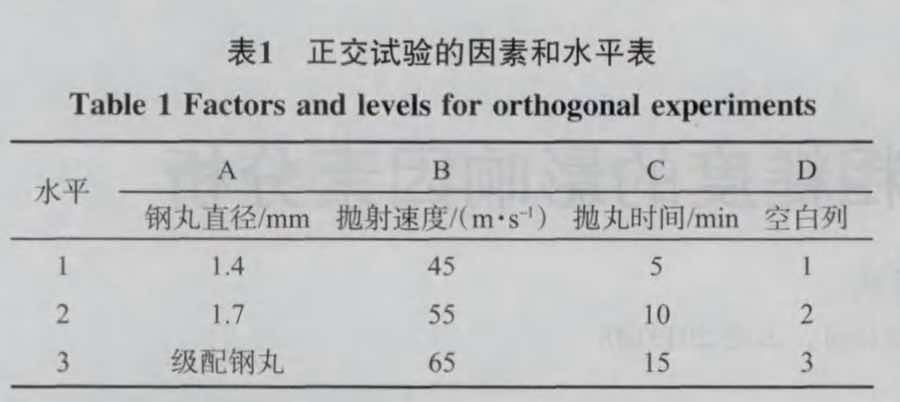
2试验结果及分析
抛丸清理结束后,取铸件有代表性的三个表面,如图1a,观察并测量表面粗糙度数值。根据GB/T6060.1-1997,将铸件表面与粗糙度比较样块进行对比,发现9组试验的铸件表面粗糙度均位于R-12.5um~25 um区间,抛丸清理达到了应有的效果。用粗糙度测试仪测量铸件A、B.C三个面的粗糙度,并取平均值,结果如表2。

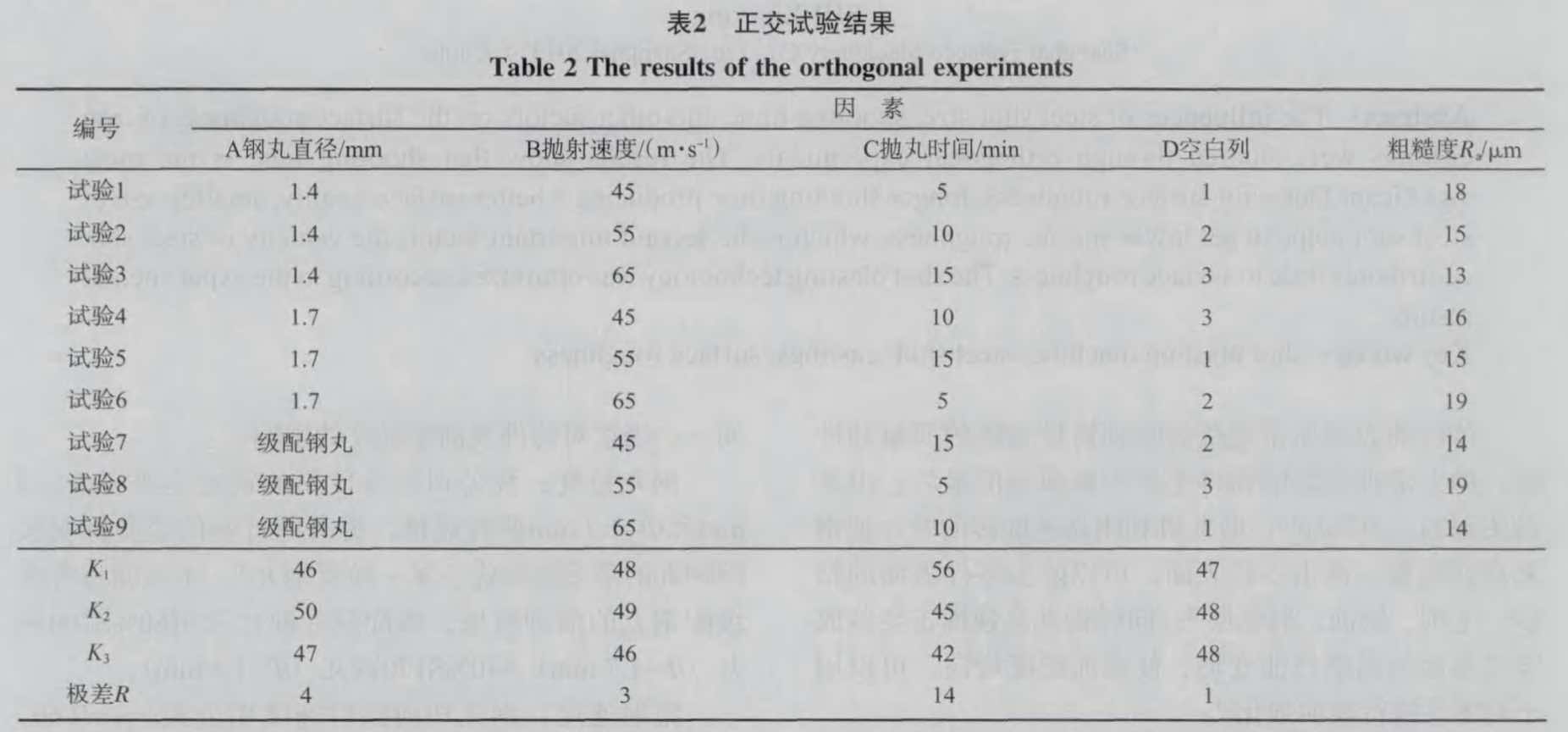
分析得知,最优方案为CA,B,即抛丸时间15min、钢丸直径1.4 mm、抛射速度65 m/s;由于C列极差远远大于其他各列,表明抛丸时间对粗糙度的影响最显著。由于D列极差R的数值仅为1,可以认为在现有的试验条件下,不存在其他对铸件表面粗糙度影响显著的未知因素。
将试验中的三个因素的水平为横坐标,以R的平均值k-K/3为纵坐标,得到表面粗糙度R,与各因素的变化趋势图(图2)
分析表明,随着抛丸时间的增加,铸件表面粗糙度R,逐渐降低,但是从10min到15 min这段时间,R降低的趋势远低于5 min到10 min时间段,前人的相关研究也有类似的结果;考虑到生产成本,实际生产中完全可以将抛丸时间定为10 min。
采用60%4-1.7 mm钢丸+40%0-1.4 mm钢丸混合成的级配钢丸,对降低粗糙度的作用不明显,由于1.7mm钢丸的存在, R,明显高于1.4 mm钢丸的方案;但是通过正交试验的结果来看,级配钢丸可以一定程度上缩短抛丸的时间,在以后的生产和研究中有必要做进一步探索。
Ra随钢丸抛射速度的变化很小,由于试验中抛射速度的取值基本在该抛丸机推荐的抛射速度范围,可以认为,在该范围内,钢丸抛射速度对铸件最终的表面粗糙度无明显影响。
3结论
研究结果表明:抛丸时间对铸件表面粗糙度的影响最大,抛丸时间越长,铸件表面粗糙度越低;其次为钢丸粒度,直径较小的钢丸有利于降低表面粗糙度;而钢丸抛射速度的影响较小。
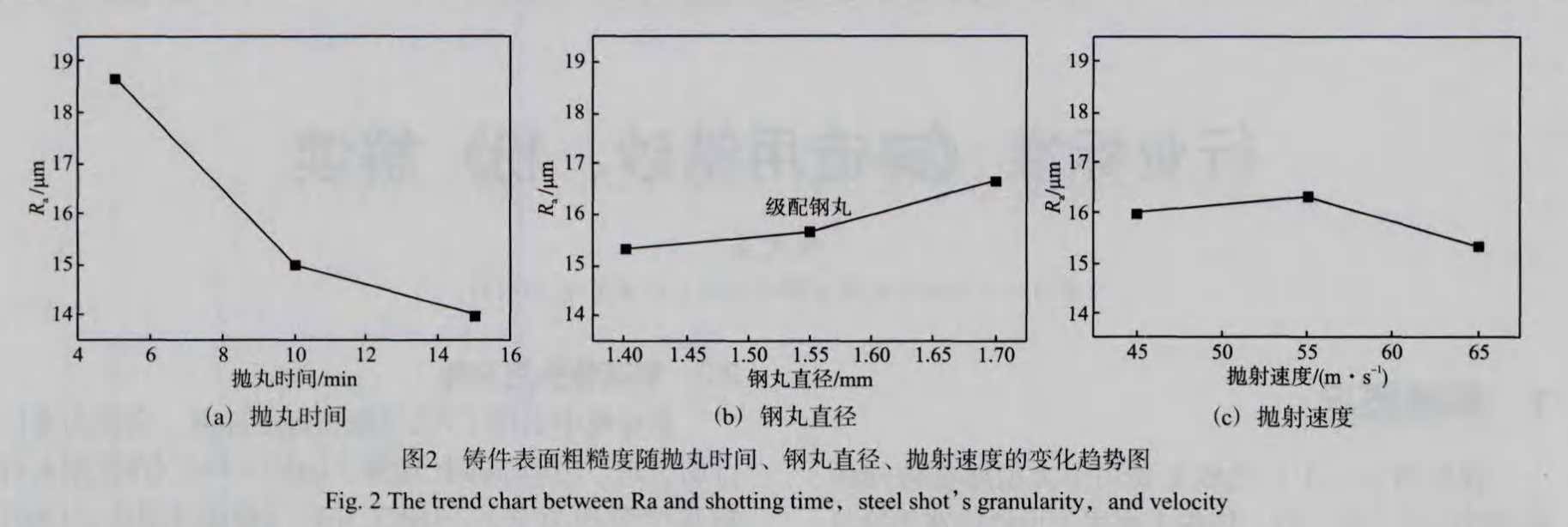
考虑到生产成本,抛丸时间并非越长越好,对于中等箱体铸铁件,采用 =1.4 mm的钢丸清理10 min,能在保证清理效率的同时达到较好的抛丸效果。
江苏抛丸清理设备制造厂家,为您提供专业的抛丸机设备和抛丸工艺技术服务!
喷抛丸设备、喷丸强化技术服务,182 0189 8806 文章链接:http://www.shot-peening.cn/1758/